.jpg)
Manufacturing ERP Software
Our’s dedicated ERP manufacturing software offers world-class capabilities that drive digital transformation for smart & agile manufacturing operations, adapted for Industry 4.0.
Manufacturing ERP is software for manufacturing businesses of all sizes. Manufacturing businesses need ERP with industry-specific features and capabilities to manage, automate, track, collaborate, and connect every step of their dynamic manufacturing processes, from the receipt of a customer order to the shipment and delivery of the order.
A manufacturing company, be it small or large can benefit from ERP systems in many ways. It is imperative for modern manufacturing companies to use solutions and tools that help them accelerate growth and establish data-driven culture to make informed decisions at every step.
Manufacturers May Operate in One or More Modes:
- Make to stock: Make products in anticipation of orders yet to come.
- Make to order: Make products to fulfill orders received.
- Engineer to order: Make a product that is designed, engineered and finished after an order has been received.
- Customize to order: Customize standard orders to customer requirements or specifications.
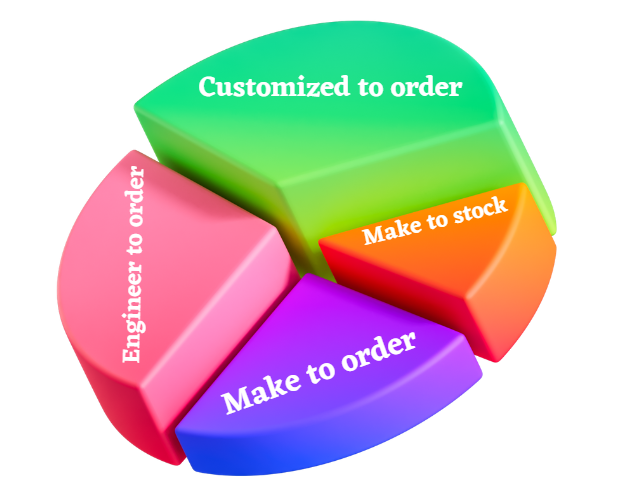
What are Common Manufacturing ERP Features?
Bill of Materials (BOM) and Routing
A bill of material is at the heart of any cloud manufacturing software, and a well-defined BOM ensures robustness and accuracy. ERPNext's BOM is hierarchical, with the finished product at the top. It also includes product codes, part descriptions, quantities, costs, routing and additional specifications.
Material Requirements Planning (MRP)
MRP system that helps businesses manage their manufacturing processes by determining the materials, quantities, & timing required for production. MRP analyzes production schedules, inventory levels, & lead times to ensure the necessary materials are available when needed. It automates planning & management, reduces waste, optimizes inventory levels, & improves productivity.
Production Management
This feature enables manufacturers to plan and schedule their production processes by optimizing resources, such as labor, materials, and equipment. Overall, this feature help manufacturers improve efficiency, reduce costs, & optimize their production processes to meet customer needs & drive business growth.small
Master Production Scheduling (MPS)
This feature is used in manufacturing businesses to determine the production schedule for finished goods. It involves forecasting customer demand, analyzing inventory levels, and creating a production plan to meet that demand while optimizing resources such as labor, materials, and equipment.
Batched & Serialized Manufacturing
With ERPNext's integrated inventory, managing batched & serial number of items is simple. Its real-time view of product availability maintains each batch's manufacturing dates, expiration dates, and serial no. details. You can even scan item barcodes with your device camera to quickly search through your stock and make data-driven decisions.
Integration with Plant Floor Machinery
With ERPNext's job cards, operations and workstations features, you can automatically capture daily activities on your shop floor. View real-time status of the job work being done to manufacture products, the location of every workstation, employee assignments, and each work order's current status and pending steps — all in one screen.
Why is Manufacturing ERP Important for Manufacturing Business?
- Track raw materials, allocate resources and plan out the production process.
- Manage the manufacturing process more efficiently from start to finish, while tracking shop floor activities.
- Schedule jobs based on raw materials in stock, by machine time and labor hours.
- Manage daily finances, create custom reports and track job costing.
- Centralized data storage and safe access to data based on roles.
- Reduced cost and operational overhead of using single software.
- Accurate demand forecasting through advanced analytics and BI.
- Well-defined product life-cycle management.
- Better adherence to compliance and regulatory standards.
- Monitor inventory of finished goods coming in and going out.
- Receive, scan in and store products, knowing the location of each item within the warehouse.
- Use quality control check points to ensure products meet customer specifications.
- Real-time reporting and dashboards that help make better decisions timely.
- Ultimately helps improve customer satisfaction and customer services.
- Quick resolution of any issue with advanced alert management and collaboration.
- Mitigate risks and minimize redundancy and human errors.
- Respond to market changes and conditions quickly than ever.